Introduction
With the advent of 3-D printing, structurally complex objects that were once unbuildable can now be easily manufactured. However, what if these objects could be designed and manufactured to respond or change in predictable or pre-programmed ways to a stimulus applied after their production? Enter 4-D printing.
The term “4-D printing” was coined in February 2013 [1]. The first academic paper to address the concept appeared seven months later [2], describing how 3-D printing techniques can combine with active or smart materials to form 4-D printed objects whose shape, properties, and functionalities can be deliberately changed after printing [3,4]. 3-D printing is a process of rapidly creating three-dimensional objects in a layer-by-layer fashion. Today, many different technologies exist to implement 3-D printing, including powder bed laser melting (where material powders are melted by a raster laser to form a layer of solid material with a well-defined geometry) and vat photopolymerization, which takes a layer of polymer resin and converts it to a layer of solid by a raster laser or a projector. Figure 1 depicts another method, polyjet 3-D printing technology, which is used by researchers in the Mechanics of Soft Materials Laboratory at Georgia Institute of Technology (Georgia Tech). In this method, several inkjet print heads are used to jet different polymer resins (in a manner similar to how different color inks are jetted onto paper in an inkjet printer), after which the resin is cured (or solidified) using ultraviolet light.
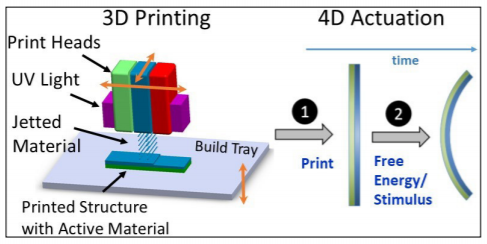
Figure 1: Illustration of actuation of a 4-D printed object upon stimulus after a standard (polyjet) 3-D printing process. Adapted from [10]
4-D printing typically uses two or more materials, at least one of which is active and can respond to a trigger stimulus. Active, or smart materials, include a wide variety of substances that can change their appearance, material properties, and/or shape in a controlled manner in response to an external stimulus. Here, “active” or “smart” refers to the fact that these materials can “sense” their environment, so to speak, reacting to changes in environmental conditions such as temperature and/or humidity change or ultraviolet irradiation. Based on the type and intensity of the trigger stimulus, smart materials can change their physical state, such as deforming from the shape in which the material was manufactured into a different shape—one programmed in advance by a human operator.
To date, two types of active materials are under investigation for use in 4-D printing: shape memory polymers (SMPs) and hydrogels. SMPs are used in 3-D printing layered composite structures—also known as printed active composites (PACs)—that contain multiple families of shape memory polymer fibers [2]. Through proper design of the distributions of SMP fibers in the non-SMP matrix, many interesting shape changing properties can be achieved [7,21]. Hydrogels that swell in water or in solution can also be used to produce shape change when used alongside a non-swelling polymer, which converts the swelling force into a biased mechanics field [14,22]. Research into 4-D printing applications has already accomplished one-way activation in an object from an initial, programmed state, into a permanent final state [2]. Subsequent research has allowed for the programming of multiple activation states within a single composite structure [19], and only in the past year have we begun to achieve fully-reversible two-way actuation [17].
These capabilities, combined with the typical advantages offered by 3-D printing (such as agile manufacturing), make 4-D printing a potential future solution for many Department of Defense (DoD) applications that must confront unpredictable conditions and can be strictly constrained by space, logistics, and limited resources (e.g., electrical power). For example, 4-D printing can aid in the fabrication of sensors with multiple stimulus-responsive groups, able to notify warfighters to changing ambient conditions or the presence of an imminent danger [23], active truss structures capable of gigantic shape change that can be used as free-standing, self-assembling tents or as platforms for 4-D electromagnetic devices (like morphing antennae) [24], or soft micro-robots that can be fabricated for therapeutic drug delivery to a specific location [25,26].
There are numerous opportunities for fabricating smart structures through 4-D printing. In this article, we discuss several projects recently completed by our research group at the Georgia Tech and a team of collaborators, starting with the use of SMPs in printed active composites that require thermomechanical programming to induce shape change. We then discuss how internal stress-induced shape changes can be used in 4-D printing, and how objects can transform directly off the print bed. Finally, recent progress with the use of hydrogels as active materials is examined. In each section we use these projects to illustrate the immense potential that 4-D printing has for a wide array of DoD applications. Printed Active Composites
As discussed above, 3-D printing allows for the placement or fusion of different materials into one object to form a composite. When one material is an active material, the composite largely inherits the “smart” nature of the active material, while the specific parameters of those active motions in the composite object are determined by how the active and non-active materials interact; this offers 4-D printed objects a high amount of tunability [8,19,27]. Polyjet printing technology allows for printing SMPs with different glass transition or activation temperatures, and thus can be used to create active components [21]. An SMP is a polymer that can be programmed (or formed) into a temporary shape and later made to recover its permanent shape upon exposure to its trigger stimulus [28].
To date, temperature is the most commonly used trigger stimulus in SMP-focused studies. In a typical application, the SMP can be programmed into a shape through a thermomechanical loading process in which the SMP is first heated to above its transition temperature (such as glass transition), deformed, and then cooled. Upon unloading at the low temperature, the SMP remains in the temporary, deformed shape. To recover its permanent shape, the SMP is heated to a temperature above the transition temperature. It should be noted that the shape change from temporary to permanent in this example is a one-time event (i.e., the SMP would have to be programmed again by the thermomechanical deformation). However, there are research efforts underway to make multi-use reversible shape changes possible [29,30].
Figure 2A depicts an example of a printed active composite using an SMP that results in bending. This PAC laminate consisted of a single layer of SMP fibers in a soft matrix. After printing, the PAC was programmed with a simple thermal-mechanical programming step (including stretching at a high temperature, cooling to a low temperature (0 C), and releasing the mechanical load), and the PAC object was bent. The resulting bending can be used to create active origami structures such as the self-folding airplane shown in Figure 2B. The 4-D printed active origami structures demonstrated their ability to solve engineering issues related to the packing of large structures into small volumes, for purposes related to storage and transportation. Additionally, this folding/assembling process that was triggered by a stimulus and executed automatically (self-folding or self-assembling) has the advantage of being able to overcome the limitation of requiring manpower to work in extreme environments or urgent/dangerous situations. For example, a printed flat pack structure could deploy into a three-dimensional structure by applying the trigger stimulus, producing, for example, a self-foldable building or tent for immediate use in the field [24]. For another example, the hydrogel-based shape-shifting structures can be used as a rain-expandable structure requiring minimal human involvement to utilize [31].
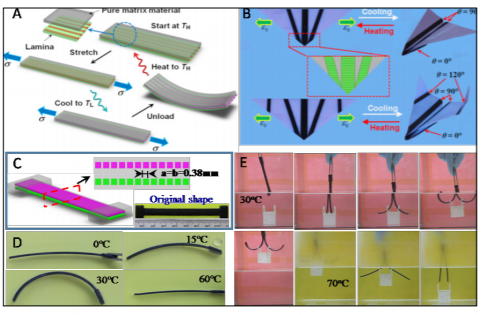
Figure 2: 4-D printing of SMP composites. (A) Schematic of the design, programming step, and shape memory cycle of a single-layer fiber-matrix composite [2]. (B) Active origami airplane utilizing the active hinges [33]. (Released) (C) The design of the composite structure
with two layers of different SMP fibers embedded inside the rubbery matrix. (D) The shape changing behavior of the printed and programmed composite at different temperatures. (E) A smart hook application of the SMP composite
PACs do have some limitations. For example, the PACs illustrated in Figure 2 are successful in creating active structures; however, they require extensive programming using the multiple-step thermal-mechanical process (including heating, deforming, cooling, and removing load) before actuation. In addition, the actuation is single-use; achieving reversible or two way shape change would require special designs or mechanisms. Direct 4-D Printing Using
Printed Active Composites
Recently, our research group and collaborators developed a new method such that a composite can be directly activated and made to maintain a new shape through simple heating [10]. Here, we utilized the
residual strain induced during 3-D printing, which was controlled by the material composition and printing process parameters. When a laminated strip with an SMP in conjunction with an elastomer was printed (the printing method is similar to the one used in the PAC discussed above), the elastomer was imbued with the residual strain created by the 3-D printing process. After it was removed from the printing tray and heated, the laminate object bent due to the residual strain and the thermal expansion mismatch of the two materials (see Figure 3A). This new bent shape is permanent; the strip would not change upon further cooling and heating after it was first bent.
This simple bending process could be used to create more complex shape changes, such as the expanding lattice shown in Figure 3B or the shrinking lattice shown in Figure 3C. The difference between Figure 3B and Figure 3C lies in where the elastomers are placed, which indicates the large degree of design freedom that 3-D printing offers. Figure 3D depicts a 4-D printed object that was designed to be printed flat but raises up and expands to form a dome upon heating. In Figure 3E, initially flat petals bend and form a closing flower.
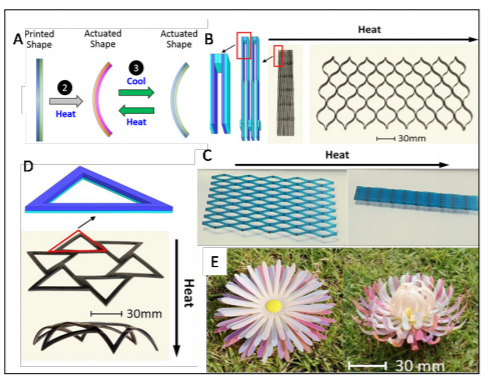
Figure 3: (A) The concept of direct 4-D printing where two layers of different materials are printed together, and the difference of the thermal expansion coefficients and the printing-induced internal strain can induce shape changing behavior (B) A lattice structure that expands greatly upon heating (C) A lattice that can shrink upon exposure to heat (D) A flat structure that can expand upon heating to create a dome structure (E) Printed flower blooms into a configuration where petals at different layers assume final configurations with different curvatures. Adapted from [10].
Internal Shrinkage, Stress-Induced Shape Change
Volume shrinkage is a common event when a polymer is cured (changed from a liquid resin to a solid polymer); therefore, it occurs in many 3-D printing processes, especially when photopolymerization is used. Volume shrinkage in general should be avoided in 3-D printing techniques, as it can cause shape distortion if the geometry of the printed part is especially complex. However, if such a volume change can be precisely controlled, its occurrence can be advantageous for creating shape-changing structures [11,34].
Our research group developed a simple method to fabricate thin film structures by utilizing the volume shrinkage stress induced during the photopolymerization process [35] (see Figure 4A). A commercial projector was used as the light source. Photoabsorbers were added into the resin to attenuate the light, creating a light intensity gradient across the thickness direction within the liquid resin. Therefore, the material directly exposed to the light (the bottom of the resin shown in Figure 4A) was cured faster than the material further from the light, resulting in a nonuniform volume shrinkage and stress gradient in the cured polymer. Once the material was removed from the curing stage, the cured polymer sheet was activated and bent toward the less cured portion (the top surface in Figure 4A).
Further experiments demonstrated that the bending curvature depended on the illumination energy, which can be controlled by the intensity of the light, the length of illumination, or both (see Figure 4B). The light intensity was related to the grayscale in the CAD drawing; as a result, by precisely controlling the spatial distribution of the designed grayscale pattern, we easily created complex 3-D origami structures. Figure 4C illustrates a flat polymer sheet after photopolymerization (using the pattern in the inset), and Figure 4D illustrates the bending shape achieved after removal from the printing stage. Complex polyhedron structures may also be fabricated, as illustrated in Figures 4E and 4F.
To extend the application of this method, a two-sided illumination procedure was proposed, as illustrated in Figure 4G. After the first illumination step, the material was flipped, and a second gray level pattern was projected. Using this method, origami structures that require bending deformation toward different directions can be printed (see Figure 4H). One advantage of this method is that it can quickly produce 3-D printed, thin film structures by using a commercial projector. One potential application is to fabricate contact lenses, as illustrated in Figure 4I. It should be noted that this method creates shape changes that are currently irreversible and single-use only. Recently, we extended this method to program reversible shape changes into objects by tuning the materials used in this approach [11].
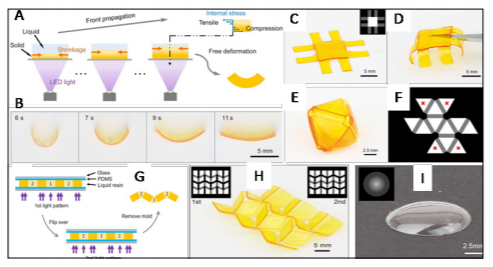
Figure 4: (A) Schematic of volume shrinkage–induced bending (B) The bending deformation of the samples controlled by the irradiation times (C) Polymer sheet directly after photopolymerization (D) Free bending shape of (C). (E)-(F) A polyhedron created by one-side illumination using light pattern shown in (F). (G) Using two-side illuminations to fabricate more complex origami structures (schematic). (H) Origami structure created by the two-side illumination method. (I) Contact lens fabricated using a commercial projector as the light exposure source.
Hydrogel for 4-D Printing of Reversible Shape Changing Structures
Some highly absorbent materials, such as hydrogels, yield large volume changes upon introduction to solvents in a process called swelling. The swelling and de-swelling behavior of hydrogels can be used to force shape change in 4-D printed structures [5,7,20]. However, one disadvantage of hydrogels is their softness, with Young’s modulus in the range of a few tens to hundreds of kPas (although their bulk modulus could be very high).
In 2015, our research group developed a new design that utilized the swelling of a hydrogel as the driving force and the temperature dependent modulus change of a SMP as a switch to create shape change components capable of being stiff in two different configurations [7]. Figure 5A illustrates a design in which the hydrogel was sandwiched between an SMP layer and an elastomer layer. The elastomer was also deposited in columns to convert the hydrogel’s swelling to in-plane expansion. Figure 5B illustrates the deformation process. The hydrogel sample was first printed according to the design in Figure 5A. It was then immersed in cold water (~0 C) for ~12 hours (see S1 in Figure 5B), allowing the hydrogel to absorb water. Because the temperature was low, the SMP had a very high modulus, which prevented the strip from deforming. The strip was then moved to a hot water bath (see S2 in Figure 5B). The modulus of the SMP strongly depended on temperature. Because of the temperature rise, the modulus of the SMP dropped by approximately three orders of magnitude, which led to a quick bending of the strip (typically within 10–20 seconds). The strip was removed from the hot water bath (see S3 in Figure 5B), and it remained in the bent shape. The strip was then left to dry in a low temperature environment (see S4 in Figure 5B). The resulting dehydrated strip was stiff—able to support a load of 25 grams. When the strip was heated again, it returned to its straight, unbent shape.
This process could easily be used in more complicated designs. For example, our research team also printed a flower design (see Figure 5C). The flower closed its petals once immersed in cold water. The flower also carried a load of 25 grams at low temperature (see Figure 5D). This new design was capable of reversible shape changes, fast deployment speeds (within ~10 seconds), and a high degree of stiffness. This makes it a good candidate for DoD applications, such as for use in micro unmanned aerial vehicles (UAVs) or small UAVs (SUAVs) for surveillance. For example, the aforementioned steps (see S1–S4 in Figure 5B) could be performed on an SUAV promptly after fabrication. The SUAV could then be deployed into a flying configuration once activated by temperature (set either to an environment change or through remotely controlled electrical heating).
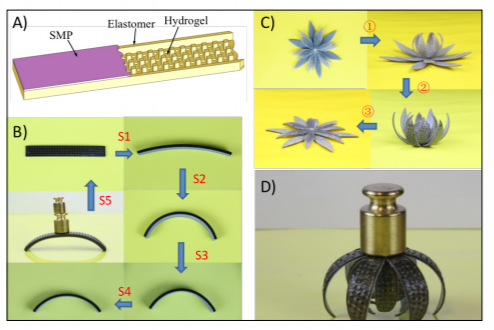
Figure 5: Hydrogel based design for 4-D printing applications. (A) The schematic graph of the design concept where the hydrogel is sandwiched between an SMP layer and an elastomer layer. The elastomer is also used in columns to convert the volume deformation of hydrogel swelling to in-plane expansion. (B) The experimental process showing the deformation. The
deformed structure is stiff and can carry a 25g load. (C) The design can be used for a flower (D), which can be very stiff to carry a 25g load
Future Possibilities
The field of 4-D printing is rapidly developing. It enables the targeted evolution of a 3-D printed structure’s shape, property, and functionality over time through the use of printable active materials. This article discussed several recently developed and facilely approached methods from our research group and collaborators, including shape-memory polymer-based unconstrained-thermo-mechanics; internal stress-based constrained-thermo-mechanics; and hydrogel-based hydro-mechanics. The use of active materials, realized through 3-D printing, enables innovative applications previously unachievable by conventional manufacturing processes. For example, potential military applications for 4-D printed hydrogel structures could be pursued in key areas including, but not limited to, improved battlefield medical devices for wound healing [36,37], drug delivery systems [38], wearable electronics [39], and energy-storing supercapacitors [40]. However, as with any emerging field of research and development, 4-D printing still faces many challenges. Each class of potential applications presents a different set of requirements that the material system must satisfy. For instance, biomedical devices must be fabricated from a bio-compatible polymer so that they may be introduced into the body without triggering harmful response [41,42]. Similarly, a major roadblock in the widespread implementation of flexible, wearable electronics is the lack of a proper energy storage system that can withstand constant mechanical deformation from the wearer’s movement [43]. Another challenge associated with 4-D printing is that most printing processes deploy thin structures in order to produce a large shape change relative to their size. Although thin structures are routinely pursued in DoD applications for lightweight equipment, it will also be important to achieve shape change in large, thicker structures for more durable applications. Therefore, it is necessary for the 4-D printing processes discussed in this article to be closely tailored to a given structure’s end-use applications and environmental requirements.
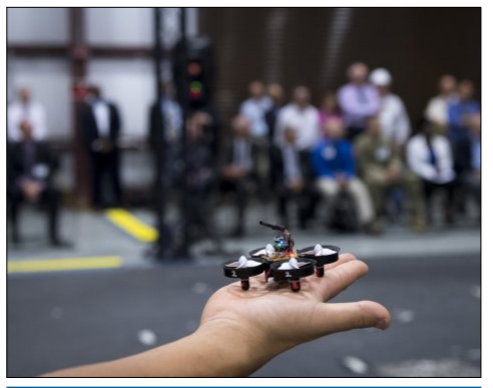
Figure 7: This is an example of a mini-UAV. This mini-UAV was developed based on a decade of research conducted by Army Research Laboratory as well as partners in academia and industry. (Source: Army Research Laboratory)
The potential benefits of using applications of 4-D objects go well beyond the feature of simple shape-shifting. Other stimulus-responsive properties, such as self-healing and self-sensing, are beginning to be incorporated into 4-D printed structures [44-46]. Further types of application may be brought to fruition if this technology is implemented with other advances, such as color-shifting textiles intended to help warfighters conceal themselves by bending the light reflected from the clothing [47].
To better implement and maximize the potential applications of 4-D printing, further research should be aimed at developing novel, stronger, and more durable printable active materials, and producing new 4-D printing concepts and predictive design tools based on theory. With these efforts, 4-D printing may become beneficial for many future DoD applications.
References
1. Tibbits, S. (2013, February). The emergence of “4D printing” [Video]. Presented at TED2013. Video retrieved from https:// www.ted.com/talks/skylar_tibbits_the_emergence_of_4d_printing
2. Ge, Q., Qi, H. J., & Dunn, M. L. (2013). Active materials by four-dimension printing. Applied Physics Letters, 103(13), 131901. doi:10.1063/1.4819837
3. Tibbits, S. (2014). 4D printing: Multi-material shape change. Architectural Design, 84(1), 116-121. doi:10.1002/ad.1710
4. Pei, E. (2014). 4D printing: Dawn of an emerging technology cycle. Assembly Automation, 34(4), 310-314. doi:10.1108/aa-07-2014-062
5. Raviv, D., Zhao, W., Mcknelly, C., Papadopoulou, A., Kadambi, A., Shi, B., . . . Tibbits, S. (2014). Active printed materials for complex self-evolving deformations. Scientific Reports, 4(1). doi:10.1038/srep07422
6. Jamal, M., Kadam, S. S., Xiao, R., Jivan, F., Onn, T., Fernandes, R., . . . Gracias, D. H. (2013). Bio-origami hydrogel scaffolds composed of photocrosslinked PEG bilayers. Advanced Healthcare Materials, 2(8), 1142-1150. doi:10.1002/adhm.201200458
7. Mao, Y., Yu, K., Isakov, M. S., Wu, J., Dunn, M. L., & Qi, H. J. (2015). Sequential self-folding structures by 3D printed digital shape memory polymers. Scientific Reports, 5(1). doi:10.1038/srep13616.
8. Yu, K., Dunn, M. L., & Qi, H. J. (2015). Digital manufacture of shape changing components. Extreme Mechanics Letters, 4, 9-17. doi:10.1016/j.eml.2015.07.005
9. Zhang, Q., Zhang, K., & Hu, G. (2016). Smart three-dimensional lightweight structure triggered from a thin composite sheet via 3D printing technique. Scientific Reports, 6(1). doi:10.1038/srep22431
10. Ding, Z., Yuan, C., Peng, X., Wang, T., Qi, H. J., & Dunn, M. L. (2017). Direct 4D printing via active composite materials. Science Advances, 3(4). doi:10.1126/sciadv.1602890
11. Zhao, Z., Wu, J., Mu, X., Chen, H., Qi, H. J., & Fang, D. (2016). Desolvation induced origami of photocurable polymers by digit light processing. Macromolecular Rapid Communications,38(13), 1600625. doi:10.1002/marc.201600625
12. Zhao, Z., Wu, J., Mu, X., Chen, H., Qi, H. J.,
& Fang, D. (2017). Origami by frontal photopolymerization. Science Advances, 3(4).
doi:10.1126/sciadv.1602326
13. Laflin, K. E., Morris, C. J., Muqeem, T., & Gracias, D. H. (2012). Laser triggered sequential folding of microstructures. Applied Physics Letters, 101(13), 131901. doi:10.1063/1.4754607
14. Gladman, A. S., Matsumoto, E. A., Nuzzo, R. G., Mahadevan, L., & Lewis, J. A. (2016). Biomimetic 4D printing. Nature Materials,
15(4), 413-418. doi:10.1038/nmat4544 15. Bakarich, S. E., Gorkin, R., Panhuis, M. I., & Spinks, G. M. (2015). 4D printing with mechanically robust, thermally actuating hydrogels. Macromolecular Rapid Communications, 36(12), 1211-1217. doi:10.1002/ marc.201500079
16. Kuksenok, O., & Balazs, A.C. (2016). Stimuli-responsive behavior of composites integrating thermo-responsive gels with photo-responsive fibers. Materials Horizons, 3(1), 53-62.
17. Yuan, C., Roach, D. J., Dunn, C. K., Mu, Q., Kuang, X., Yakacki, C. M., . . . Qi, H. J. (2017). 3D printed reversible shape changing soft actuators assisted by liquid crystal elastomers. Soft Matter, 13(33), 5558-5568. doi:10.1039/c7sm00759k
18. Naficy, S., Gately, R., Gorkin, R., Xin, H., & Spinks, G. M. (2016). 4D printing of reversible shape morphing hydrogel structures. Macromolecular Materials and Engineering, 302(1), 1600212. doi:10.1002/mame.201600212
19. Wu, J., Yuan, C., Ding, Z., Isakov, M., Mao, Y., Wang, T., . . . Qi, H. J. (2016). Multishape active composites by 3D printing of digital shape memory polymers. Scientific
Reports, 6(1). doi:10.1038/srep24224
20. Lewis, J.A. (2006). Direct ink writing of 3D functional materials. Advanced Functional Materials,16(17), 2193-2204. doi:10.1002/adfm.200600434
21. Yu, K., Ritchie, A., Mao, Y., Dunn, M. L., & Qi, H. J. (2015). Controlled sequential shape
changing components by 3D printing of shape memory polymer multimaterials. Procedia IUTAM, 12, 193-203. doi:10.1016/j.piutam.2014.12.021
22. Thérien-Aubin, H., Wu, Z. L., Nie, Z., & Kumacheva, E. (2013). Multiple shape transformations of composite hydrogel sheets. Journal of the American Chemical Society, 135(12), 4834-4839. doi:10.1021/ja400518c
23. Schattling, P., Jochum, F. D., & Theato, P. (2014). Multi-stimuli responsive polymers –the all-in-one talents. Polym. Chem., 5(1), 25-36. doi:10.1039/c3py00880k
24. Liu, K., Wu, J., Paulino, G. H., & Qi, H.J. (2017). Programmable deployment of tensegrity structures by stimulus-responsive polymers. Scientific Reports, 7(1). doi:10.1038/s41598-017-03412-6
25. Huang, H., Petruska, A. J., Sakar, M. S., Skoura, M., Ullrich, F., Zhangm, Q., . . . Nelson,
B. J. (2016). Self-folding hydrogel bilayer for enhanced drug loading, encapsulation, and transport. 2016 38th Annual International Conference of the IEEE Engineering in Medicine and Biology Society (EMBC). doi:10.1109/embc.2016.7591143
26. Butvilovskaya, V. I., Popletaeva, S. B., Chechetkin, V. R., Zubtsova, Z. I., Tsybulskaya, M., Samokhina, L. O., . . . Rubina, A. Y. (2016). Multiplex determination of serological signatures in the sera of colorectal cancer patients using hydrogel biochips. Cancer Medicine, 5(7), 1361-1372. doi:10.1002/cam4.692
27. Hiller, J., & Lipson, H. (2009). Design and analysis of digital materials for physical 3D voxel printing. Rapid Prototyping Journal, 15(2), 137-149. doi:10.1108/13552540910943441
28. Behl, M., & Lendlein, A. (2007). Shape-memory polymers. Materials Today, 10(4), 20-28.
doi:10.1016/s1369-7021(07)70047-0
29. Westbrook, K. K., Mather, P. T., Parakh, V., Dunn, M. L., Ge, Q., Lee, B. M., & Qi, H. J. (2011). Two-way reversible shape memory effects in a free-standing polymer composite. Smart Materials and Structures, 20(6), 065010. doi:10.1088/0964-
1726/20/6/065010
30. Chung, T., Romo-Uribe, A., & Mather, P. T. (2008). Two-way reversible shape memory in a semicrystalline network. Macromolecules, 41(1), 184-192. doi:10.1021/ma071517z
31. Campbell, T. A., Tibbits, S., & Garrett, B. (2014). The programmable world. Scientific
American, 311(5), 60-65. doi:10.1038/scientificamerican1114-60
32. Lendlein, A., & Langer, R. (2002). Biodegradable, elastic shape-memory polymers
for potential biomedical applications. Science, 296(5573), 1673-1676. doi:10.1126/
science.1066102
33. Ge, Q., Dunn, C. K., Qi, H. J., & Dunn, M. L. (2014). Active origami by 4D printing. Smart
Materials and Structures, 23(9), 094007. doi:10.1088/0964-1726/23/9/094007
34. Huang, L., Jiang, R., Wu, J., Song, J., Bai, H., Li, B., . . . Xie, T. (2016). Ultrafast digital printing toward 4D shape changing materials. Advanced Materials, 29(7), 1605390. doi:10.1002/adma.201605390
35. Zhao, Z., Wu, J., Mu, X., Chen, H., Qi, H. J., & Fang, D. (2017). Origami by frontal photopolymerization. Science Advances, 3(4). doi:10.1126/sciadv.1602326
36. Khademhosseini, A., & Langer, R. (2016). A decade of progress in tissue engineering. Nature Protocols, 11(10), 1775-1781. doi:10.1038/nprot.2016.123
37. Holloway, J. L., Spiller, K. L., Lowman, A. M., & Palmese, G. R. (2011). Analysis of the
in vitro swelling behavior of poly(vinyl alcohol) hydrogels in osmotic pressure solution
for soft tissue replacement. Acta Biomaterialia, 7(6), 2477-2482. doi:10.1016/j.actbio.2011.02.016
38. Malachowski, K., Breger, J., Kwag, H. R., Wang, M. O., Fisher, J. P., Selaru, F. M., & Gracias, D. H. (2014). Stimuli-responsive theragrippers for chemomechanicalcontrolled release. Angewandte Chemie
International Edition, 53(31), 8045-8049. doi:10.1002/anie.201311047