“Structural batteries, i.e. those that can perform two functions at the same time – to store charge and to carry structural load, are known to effectively reduce total system weight [1,2]. This is a universal design improvement for all the devices that have potteries regardless of their size- from electric vehicles [3-8] to airplanes and satellites [4,5,8].”
For instance, combining the energy storage and load bearing functions makes possible weight reduction of an exemplary electrical vehicle by about 350 kg [3-8]. The U.S. Department of Defense (DoD) employs an increasingly sophisticated force of unmanned systems. On December 2007 Unmanned Systems Roadmap spanning 25 years was published that anticipated and projected a major shift toward greater reliance on unmanned vehicles in U.S. military operations [9,10]. The performance of all of them can benefit from the broad implementations of structural batteries and other structural power options that could be integrated in different load-bearing elements of the robotic devices from protective covers to radiator grids (Figure 1) and aerodynamic components. The need for structural batteries becomes obvious when one considers the technical challenges that robotic devices encounter in the military. For example, short flight duration is one of the main challenges of unmanned aerial vehicles (UAV) and utilization of the structural batteries can substantially improve this critical performance characteristic. Although the small lithium/polymer batteries are the best choice of power due to their capabilities to provide required high discharge current rate, most UAVs still have limited storage capacity, leading their limited flight time up to 30 minutes [11]. Initial assessments and flight tests indicate that structural batteries have the possibility to markedly extend the flight duration of UAVs and other aerial vehicles [12]. Further development of this technology can also be guided by the use of structural energy storage in biology and biomimetic design of some of the battery components.

For some time, efforts have been devoted worldwide to developing flexible, textile and stretchable energy storage devices such as supercapacitors and lithium ion batteries [13-18]. The team of researchers from Kungliga Tekniska Högskolan (KTH), Sweden successfully inserted Li ions in the carbon fiber. Their results suggested that the inserted ions created elastic strains in the fiber, which hence becomes pre-stressed in tension rather than causing irreversible damage to the carbon fiber [19]. The team of researchers from Imperial College London, United Kingdom, reported that a carbon fiber reinforced polymer composite can act as a supercapacitor whilst sustaining mechanical loads (Figure 2) with compressive moduli of up to 39 GPa and capacitances of up to 52 mF g-1 [18]. Here, we must underline the difference between energy and power density. Energy density indicates total energy stored in a given mass or volume whereas power density shows how fast stored energy is released in a given mass or volume [20]. The latter is directly related to maximum current we can apply from a given mass. Though supercapacitors have high power density (W/kg), the insufficient energy density (Wh/kg) limits their applications; batteries possess significantly higher energy density [21].
However, structural batteries and other types of structural energy storage are not a part of current technological landscape devices because of the fundamental conflict between the ability of all material to carry load and transport charge [1]. The simultaneous attainment of high ionic conductivity and high stiffness [22,23] requires opposite structural requirements in materials. High density of permanent covalent bonds is required for load carrying, while dynamic labile ionic and coordination bonds typical for fluids are needed for fast charge transport.
The same is true for high mechanical strength and high ion intercalation capacity [24] – an equally important pair of properties for structural batteries. This clash of properties can be cumulatively described as the load bearing functionality requiring strong chemical bonds and dense robust materials, whereas charge transport and storage functionalities require weak chemical bonds and porous, deformable materials.
Out-of-the-box approaches to engineering materials and devices as a whole are needed to resolve the fundamental bottleneck. It is a difficult but worthy task because the development of high capacity structural batteries without sacrificing their safety has far-reaching implications for global energy, the environment, and sustainability. For example, in UAVs the structural support around the batteries takes as much as twice the weight of a battery [25]. This additional weight imposes a high penalty on vehicle range and energy consumption [25]. Combining the load bearing and charge storage functions will, therefore, be the key factor determining flight duration for drones and other systems. Looking ahead of the technological curve, structural batteries will determine energy-based, economic viability of future mobility technologies. Using UAVs as another example, reducing the weight of piloted commercial aircraft by 1 kg results in a savings of 30 tons of fuel per year [26], illustrating the necessity and impact of structural batteries in terms of environmental problems, climate change, energy sustainability, and national security.The fundamental materials bottleneck of structural batteries can be overcome by utilizing biomimetic engineering of naturally occurring nanocomposites. The once-believed “impossible” combination of high mechanical properties and fast ionic transport necessary for the electrolyte and cathode in, for instance, Zn and Mg batteries was realized by following materials engineering blueprints made by nature when designing living tissues that combine efficient transport of nutrients and high load bearing properties [12]. These tissues were optimized over millions of years of evolution and are exemplified by articular cartilage, canalicular bones, and the dentin of teeth. All these tissues have a common basic structural motif represented by porous three-dimensional (3D) network of stiff nanoscale fibers with 20–100 nm pores (Figure 3A) [27]. Abiotic replicas of such networks (Figure 3B) have been made from aramid nanofibers that retain the exceptional mechanical properties of their precursor – the iconic ultrastrong material Kevlar® (Figure 3 C,D). Similar to their biological prototypes they can be self-assembled from individual fibers and their production is scalable.

Taking advantage of aramid nanofibers, structural batteries with Zn metal anodes, solid state Zn2+electrolytes, and mechanically robust cathodes intercalating Zn2+ ions. Rechargeable zinc ion batteries are expected to be more promising as textile power sources, owing to their combined advantages of high energy density, safety, and low cost [28-32]. Having theoretical energy densities similar to those of lithium-ion batteries [33,34], they are attractive as potential energy storage solutions for many applications.
We demonstrated that it is possible to engineer a solid Zn2+ electrolyte as a composite of aramid nanofibers. The high stiffness of the branched aramid nanofibers, BANF network combined with the high ionic conductivity of soft poly (ethylene oxide), PEO enable effective suppression of dendrites and fast Zn2+ transport. The cartilage inspired composite displays the ionic conductance 10× higher than the original polymer. The batteries constructed using the nanocomposite electrolyte are rechargeable and have Coulombic efficiency of 96-100% after 50-100 charge-discharge cycles (Figure 4).

Importantly, the metallic nature of the anodes simplifies acquisition of load-bearing capabilities [12]. High capacity rechargeable batteries with Zn metal anodes can be stamped into stiff corrugated shapes that can be fit to a specific load bearing profile (Figure 5). Zn batteries with PZB-931 were corrugated by molds (Figure 5A) with different “teeth” shaped as square (Figure 5B), half-sphere (Figure 5C), dot (Figure 5D), square wave (Figure 5E), or round wave (Figure 5F). These capabilities will open the door for numerous lightweight structural power applications. The battery voltage and capacity remained virtually unchanged, and its power showed no significant decay under a variety of deformation conditions and corrugated states. While plastic deformability has obvious limits, the constancy of the ionic conductivity spectra obtained by Electrochemical Impedance Spectroscopy (EIS) (Figure 5J) and galvanostatic charge and discharge (Figure 5I) for the studied range of deformations is remarkable.
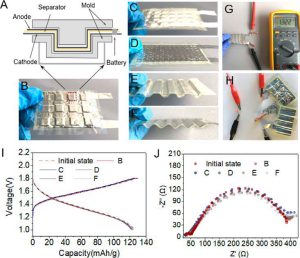
Furthermore, the biomimetic solid-state electrolyte enables the batteries to withstand not only elastic deformation during bending but also plastic deformation. This capability makes them resilient to different type of damage and enables shape modification of the assembled battery to improve the ability of the battery stack to carry a structural load. This property also suppresses formation of sharp zinc dendrites on the anode side and prevent any possible short circuit as a result of zinc metal penetration through separator during cycles. The corrugated structural batteries can be integrated into body elements of unmanned aerial vehicles as auxiliary charge storage devices (Figure 6). Taking advantage of the plastic deformability of these devices, we shaped them to replace covers of UAVs and enabled them to serve as auxiliary charge storage devices supplementing the main power source with lithium ion chemistry. The lightness of the auxiliary battery back afforded by the replacement of the liquid electrolyte with thin layers of dendrite suppressing BANF and PEO composite is essential for structural batteries in aerial vehicles. The practicality of structural batteries and significance of their shape versatility was demonstrated for several small drones of different types and power requirements. In all cases, we observed successful take off of the UAVs after their factory-installed covers were replaced with our corrugated batteries. Depending on capacity of UAVs own batteries and other parameters such as ambient temperature and size of UAVs, we calculated 5-27% of flight duration extension. The corrugated batteries were connected to the power circuits of the drones as secondary energy sources serving as structural components combining load-bearing and charge storage functions.
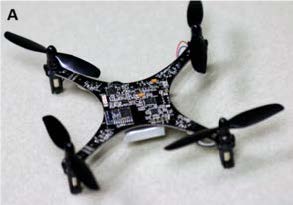

References
- González, C., Vilatela, J. J., Molina-Aldareguía, J. M., Lopes, C. S. & LLorca, J. Structural composites for multifunctional applications: Current challenges and future trends. Prog. Mater. Sci. 89, 194–251 (2017).
- Ferreira, A. D. B. L., Nóvoa, P. R. O. & Marques, A. T. Multifunctional Material Systems: A state-of-the-art review. Compos. Struct. 151, 3–35 (2016).
- Asp, L. E., Leijonmarck, S. & Carlson, T. Realisation of Structural Battery Composite. 20th Int. Conf. Compos. Mater. 19–24 (2015). doi:10.13140/RG.2.1.2029.1922
- Sairajan, K. K., Aglietti, G. S. & Mani, K. M. A review of multifunctional structure technology for aerospace applications. Acta Astronautica (2016). doi:10.1016/j.actaastro.2015.11.024
- Belvin, W. K., Watson, J. J. & Singhal, S. N. Structural Concepts and Materials for Lunar Exploration Habitats. Struct. Mater. 1–15 (2006). doi:10.2514/6.2006-7338
- Thomas, J. P. et al. Proceedings of IMECE ASME International Mechanical Engineering Congress. in 41512 1–4 (2003).
- Willgert, M. Solid Polymer Lithium-Ion Conducting Electrolytes for Structural Batteries. (2014). doi:978-91-7595-035-8
- Aglietti, G. S., Schwingshackl, C. W. & Roberts, S. C. Multifunctional structure technologies for satellite applications. Shock Vib. Dig. 39, 381–391 (2007).
- Office of the Secretary of Defence. Office of the Secretary of Defence Umanned Systems Roadmap 2007-2032. 19–20 (2007).
- Valavanis, K. P. & Vachtsevanos, G. J. Handbook of unmanned aerial vehicles. Handbook of Unmanned Aerial Vehicles (2015). doi:10.1007/978-90-481-9707-1
- Hassanalian, M. & Abdelkefi, A. Classifications, applications, and design challenges of drones: A review. Progress in Aerospace Sciences (2017). doi:10.1016/j.paerosci.2017.04.003
- Wang, M. et al. Biomimetic Solid-State Zn2+ Electrolyte for Corrugated Structural Batteries. ACS Nano (2019). doi:10.1021/acsnano.8b05068
- Liu, M. et al. Resist-Dyed Textile Alkaline Zn Microbatteries with Significantly Suppressed Zn Dendrite Growth. ACS Appl. Mater. Interfaces (2019). doi:10.1021/acsami.8b19825
- Asp, L. E. & Greenhalgh, E. S. Structural power composites. Composites Science and Technology (2014). doi:10.1016/j.compscitech.2014.06.020
- Ekstedt, S., Wysocki, M. & Asp, L. E. Structural batteries made from fibre reinforced composites. in Plastics, Rubber and Composites (2010). doi:10.1179/174328910X12647080902259
- Liu, P., Sherman, E. & Jacobsen, A. Design and fabrication of multifunctional structural batteries. J. Power Sources 189, 646–650 (2009).
- Yu, Y. et al. Co-continuous structural electrolytes based on ionic liquid, epoxy resin and organoclay: Effects of organoclay content. Mater. Des. 104, 126–133 (2016).
- Shirshova, N. et al. Structural composite supercapacitors. Compos. Part A Appl. Sci. Manuf. (2013). doi:10.1016/j.compositesa.2012.10.007
- Jacques, E., Hellqvist Kjell, M., Zenkert, D., Lindbergh, G. & Behm, M. Expansion of carbon fibres induced by lithium intercalation for structural electrode applications. Carbon N. Y. (2013). doi:10.1016/j.carbon.2013.03.015
- Aifantis, K. E., Hackney, S. A. & Kumar, R. V. High Energy Density Lithium Batteries: Materials, Engineering, Applications. High Energy Density Lithium Batteries: Materials, Engineering, Applications (2010). doi:10.1002/9783527630011
- Zeng, Y. et al. An Ultrastable and High-Performance Flexible Fiber-Shaped Ni–Zn Battery based on a Ni–NiO Heterostructured Nanosheet Cathode. Adv. Mater. (2017). doi:10.1002/adma.201702698
- Armand, M. Polymers with Ionic Conductivity. Advanced Materials 2, 278–286 (1990).
- Wang, Y. et al. Design principles for solid-state lithium superionic conductors. Nat. Mater. 14, 1026–1031 (2015).
- Jacques, E., H. Kjell, M., Zenkert, D. & Lindbergh, G. The effect of lithium-intercalation on the mechanical properties of carbon fibres. Carbon N.Y. 68, 725–733 (2014).
- Shiau, C. S. N., Samaras, C., Hauffe, R. & Michalek, J. J. Impact of battery weight and charging patterns on the economic and environmental benefits of plug-in hybrid vehicles. Energy Policy (2009). doi:10.1016/j.enpol.2009.02.040
- Steinegger, R. Fuel Economy as Function of Weight and Distance. Zürcher Fachhochschule 1–11 (2017).
- Xu, L., Zhao, X., Xu, C. & Kotov, N. A. Water-Rich Biomimetic Composites with Abiotic Self-Organizing Nanofiber Network. Adv. Mater. (2018). doi:10.1109/CEC.2008.4630985
- Parker, J. F. et al. Rechargeable nickel-3D zinc batteries: An energy-dense, safer alternative to lithium-ion. Science (80-. ). 356, 415–418 (2017).
- Xiao, X. et al. Fiber-based all-solid-state flexible supercapacitors for self-powered systems. ACS Nano (2012). doi:10.1021/nn303530k
- Ma, L. et al. Flexible waterproof rechargeable hybrid zinc batteries initiated by multifunctional oxygen vacancies-rich cobalt oxide. ACS Nano (2018). doi:10.1021/acsnano.8b04317
- Wang, R. et al. Nickel@Nickel Oxide Core–Shell Electrode with Significantly Boosted Reactivity for Ultrahigh-Energy and Stable Aqueous Ni–Zn Battery. Adv. Funct. Mater. (2018). doi:10.1002/adfm.201802157
- Zeng, Y. et al. Oxygen-Vacancy and Surface Modulation of Ultrathin Nickel Cobaltite Nanosheets as a High-Energy Cathode for Advanced Zn-Ion Batteries. Adv. Mater. (2018). doi:10.1002/adma.201802396
- Li, Y. & Dai, H. Recent advances in Zinc-air batteries. Chemical Society Reviews (2014). doi:10.1039/c4cs00015c
- Chen, X. et al. Ultrathin Co3O4 layers with large contact area on carbon fibers as high-performance electrode for flexible zinc–air battery integrated with flexible display. Adv. Energy Mater. 7, 1–11 (2017).